Industrial cabinets are the unsung heroes of countless industrial settings, quietly housing vital equipment and ensuring smooth operations. From robust steel enclosures protecting sensitive electronics to sleek stainless steel units in cleanroom environments, these cabinets are far more than just storage solutions. Their design, construction, and placement are crucial for safety, efficiency, and longevity. This guide delves into the diverse world of industrial cabinets, exploring their various types, configurations, safety considerations, and environmental impact.
We’ll examine the different materials used, comparing their strengths and weaknesses, and exploring how to choose the right cabinet for specific applications. We’ll also cover essential aspects like sizing, safety regulations, maintenance, and the overall cost-effectiveness of various options. By the end, you’ll have a solid understanding of how to select, install, and maintain industrial cabinets to maximize their performance and lifespan.
Types of Industrial Cabinets
Industrial cabinets are essential for protecting equipment, tools, and materials in various industrial settings. The choice of cabinet depends heavily on the specific application, environmental conditions, and the level of protection required. Different materials offer varying degrees of durability, corrosion resistance, and cost-effectiveness.
Several factors influence the selection of an industrial cabinet. These include the type of equipment being housed, the environmental conditions (temperature, humidity, chemicals), the required level of security, and budgetary constraints. Understanding these factors is crucial in choosing the right cabinet for optimal performance and longevity.
Material Selection and Construction Methods
Industrial cabinets are typically constructed from steel, stainless steel, aluminum, or other specialized materials. Steel cabinets are widely used due to their strength and relatively low cost. However, they are susceptible to rust and corrosion unless treated with protective coatings. Stainless steel offers superior corrosion resistance and is ideal for environments with high humidity or exposure to chemicals. Aluminum cabinets are lightweight and corrosion-resistant, making them suitable for portable applications.
Construction methods vary, from simple welded seams to more complex designs incorporating features like gasketed doors and reinforced frames.
Comparison of Cabinet Materials
Material | Durability | Corrosion Resistance | Cost |
---|---|---|---|
Steel | High | Low (unless treated) | Low |
Stainless Steel | High | High | High |
Aluminum | Moderate | High | Moderate |
Polycarbonate | Moderate | High | Moderate to High |
Types of Industrial Cabinets and Their Applications
Various types of industrial cabinets cater to specific needs. The design and features of each cabinet are tailored to protect and manage the equipment or materials within.
Type | Material | Features | Applications |
---|---|---|---|
Control Cabinets | Steel, Stainless Steel | Enclosures for control systems, often with ventilation and mounting rails. | Automation systems, process control, machinery control. Example: A robotic arm’s control system would be housed in a robust control cabinet to protect its delicate electronics. |
Electrical Cabinets | Steel, Stainless Steel | Protection for electrical components, often with grounding and safety features. | Power distribution, circuit breakers, electrical wiring. For instance, a large factory might use numerous electrical cabinets to manage its power distribution effectively and safely. |
Server Cabinets (Racks) | Steel | Structured mounting for servers, network equipment, with ventilation and cable management. | Data centers, server rooms, network infrastructure. A large telecommunications company would rely on server racks for their network infrastructure, ensuring optimal cooling and accessibility. |
Wall-Mounted Cabinets | Steel, Aluminum | Space-saving design for smaller equipment or tools. | Small workshops, offices, laboratories. A small machine shop might use wall-mounted cabinets to store smaller tools and parts, maximizing floor space. |
Cabinet Sizing and Configuration
Choosing the right size and configuration for your industrial cabinet is crucial for efficient operation and long-term reliability. A poorly sized cabinet can lead to overcrowding, overheating, and difficulty accessing components, while one that’s too large wastes valuable space and resources. Careful consideration of several factors ensures the cabinet meets your specific needs.The appropriate size and configuration of an industrial cabinet depend on several key factors.
These include the dimensions and quantity of equipment to be housed, the required space for cabling and airflow, the environmental conditions (temperature, humidity), and the overall layout of the control system. Accurate calculations are vital to prevent problems down the line.
Industrial cabinets, with their clean lines and metal accents, offer a distinctly modern aesthetic. However, if you’re looking for something with a warmer, more lived-in feel, you might consider the charm of Rustic cabinets ; but ultimately, the best choice depends on your overall design goals and the specific industrial cabinet style you have in mind. Both styles offer unique advantages for storage and visual appeal.
Internal Space Calculation
Determining the necessary internal space involves considering the dimensions of each piece of equipment and adding allowances for wiring, airflow, and future expansion. For example, if you have a PLC with dimensions of 12″ x 8″ x 6″, a power supply of 10″ x 6″ x 4″, and several sensors each occupying approximately 2″ x 2″ x 2″, you’ll need to sum these dimensions and add extra space.
Assume 1 inch of clearance around each device for airflow and cable management, and add an additional 2 inches for future expansion. This ensures adequate space for comfortable operation and maintenance. Consider also mounting brackets or rails that will take up extra space.
Total Internal Space ≈ Σ(Equipment Dimensions) + (Clearance Allowance) + (Expansion Space)
Sample Cabinet Layout
This example Artikels a cabinet layout for a small control system. The cabinet is assumed to be a standard 19-inch rack-mount cabinet.
- PLC: Mounted in the upper section of the cabinet, centrally located for easy access. This allows for convenient programming and troubleshooting.
- Power Supply: Positioned below the PLC, providing power to the PLC and other components. This ensures a stable power source for all equipment.
- Sensors (various): Mounted along the sides of the cabinet, using DIN rail or other appropriate mounting systems. This allows for easy wiring and access to each sensor. Consider labeling each sensor for clear identification.
Cable routing should be organized and labeled to facilitate maintenance and troubleshooting. Use cable ties and management systems to keep cables neat and prevent tangling. Consider leaving extra space in the cabinet for future additions or modifications. This is crucial for future flexibility and upgrades. In this design, cables are routed along the sides and rear of the cabinet to the terminal blocks.
Industrial cabinets are known for their robust construction and practicality. However, if you need something more sophisticated for a high-end setting, check out the stunning options available at High-End Cabinetry Solutions for a truly elevated look. Then, consider how those refined design elements could inspire a new take on even your most utilitarian industrial cabinets.
Safety and Regulatory Compliance
Industrial cabinets, while seemingly simple structures, require careful consideration of safety and regulatory compliance to ensure the protection of personnel and equipment. Ignoring these aspects can lead to serious accidents, equipment damage, and costly downtime. This section details crucial safety standards, potential hazards, and mitigation strategies.
Industrial cabinets, with their rugged charm, offer a unique aesthetic. However, if you’re looking for something a bit more sleek and contemporary for your workspace, check out the stylish options available at Modern Office Cabinets. While industrial cabinets provide durability, modern designs often prioritize space optimization and a cleaner look, ultimately both styles offer practical storage solutions depending on your needs.
Meeting relevant safety standards is paramount for the design, installation, and use of industrial cabinets. These standards address various aspects, from the cabinet’s physical construction to its electrical characteristics and environmental protection. Failure to comply can result in legal repercussions and invalidate insurance claims.
NEMA Ratings and Environmental Protection
NEMA (National Electrical Manufacturers Association) ratings define the degree of protection offered by an enclosure against environmental factors like dust, moisture, and corrosion. Choosing the appropriate NEMA rating is crucial for ensuring the cabinet’s contents are safe from damage. For example, a cabinet housing sensitive electronics in a humid environment might require a NEMA 4X rating, which provides protection against water and corrosion.
Conversely, a cabinet in a dry, clean environment might only need a NEMA 1 rating, offering basic protection against contact with the enclosed equipment. Selecting the incorrect rating can lead to equipment failure and potential safety hazards.
Grounding and Electrical Safety
Proper grounding is essential for preventing electrical shocks and protecting against equipment damage. Industrial cabinets must be effectively grounded to dissipate any stray electrical currents. This typically involves connecting the cabinet’s metal frame to a reliable earth ground using appropriate grounding wires and connectors. The grounding system should be regularly inspected and maintained to ensure its effectiveness.
Failure to properly ground a cabinet can result in dangerous electrical shocks or damage to sensitive electronics. Furthermore, grounding requirements often vary based on local regulations and the specific application.
Ventilation and Heat Dissipation
Excessive heat buildup within an industrial cabinet can damage sensitive electronic components, potentially leading to malfunctions or fires. Adequate ventilation is crucial for maintaining optimal operating temperatures. Methods for achieving optimal thermal management include using fans, heat sinks, and proper cabinet design to promote airflow. For instance, cabinets with perforated panels or louvers allow for natural convection cooling.
In cases where natural ventilation is insufficient, fans can be integrated to actively circulate air within the cabinet. The selection of appropriate cooling methods depends on factors like the heat generated by the equipment, the ambient temperature, and the cabinet’s size. Neglecting thermal management can result in premature equipment failure, safety hazards, and increased maintenance costs.
Potential Hazards and Safety Precautions, Industrial cabinets
Several potential hazards are associated with industrial cabinets. These include:
- Electrical hazards: Improper grounding, damaged wiring, and exposed live components can lead to electric shocks.
- Mechanical hazards: Sharp edges, moving parts, and heavy doors can cause injuries.
- Chemical hazards: Storage of hazardous materials within the cabinet requires appropriate containment and labeling.
- Fire hazards: Overheating components, flammable materials, and inadequate ventilation can increase the risk of fire.
Mitigating these risks requires implementing comprehensive safety precautions, including regular inspections, proper lockout/tagout procedures, clear warning labels, and appropriate personal protective equipment (PPE).
Maintenance and Repair
Keeping your industrial cabinets in top condition is crucial for ensuring the safety and longevity of your equipment and operations. Regular maintenance prevents costly repairs and downtime, while a proactive approach to troubleshooting minimizes disruptions. This section details preventative maintenance schedules and strategies for addressing common issues.
Preventative Maintenance Schedule
A comprehensive preventative maintenance schedule should be implemented to extend the lifespan of your industrial cabinets and minimize unexpected failures. This schedule should be tailored to the specific environment and usage of your cabinets, but a general guideline is provided below. Remember to always consult the manufacturer’s recommendations for your specific cabinet model.
- Daily Inspection: Visually inspect the cabinet for any signs of damage, loose components, or unusual noises. Check for any signs of overheating, such as discoloration or warping.
- Weekly Inspection: Check all electrical connections for tightness and corrosion. Inspect hinges, latches, and seals for proper operation and wear. Clean any dust or debris accumulated on the cabinet’s exterior and interior.
- Monthly Inspection: Perform a more thorough inspection, including checking the grounding system and testing any safety interlocks or emergency shut-off mechanisms. Lubricate moving parts as needed, following manufacturer’s instructions.
- Annual Inspection: Conduct a complete inspection, including a detailed examination of internal components, wiring, and ventilation systems. Consider professional maintenance for complex systems or specialized equipment housed within the cabinets.
Troubleshooting Common Problems
Identifying and addressing problems promptly is key to minimizing downtime and preventing further damage. Here are some common issues and troubleshooting steps:
- Malfunctioning Components: If a component within the cabinet malfunctions (e.g., a faulty fan, broken lock), isolate the problem and replace the faulty component. Always disconnect power before working on any electrical components. Refer to the manufacturer’s documentation for replacement procedures.
- Loose Connections: Loose electrical connections can lead to overheating and malfunctions. Tighten any loose screws or terminals, ensuring a secure connection. If corrosion is present, clean the connections with a suitable contact cleaner and apply a protective coating if necessary.
- Overheating: Overheating can be caused by several factors, including inadequate ventilation, faulty components, or excessive load. Check ventilation systems for obstructions, inspect components for proper function, and ensure the cabinet’s load capacity is not exceeded. If overheating persists, consult a qualified electrician.
Repairing or Replacing Damaged Parts
Repairing or replacing damaged parts requires careful planning and adherence to safety procedures. Before beginning any repair, always disconnect the power supply and ground the cabinet to prevent electrical shock.
- Minor Repairs: Minor repairs, such as replacing a damaged door handle or fixing a loose hinge, can often be accomplished with basic tools. Always ensure the replacement part is compatible with the cabinet and follow manufacturer’s instructions.
- Major Repairs: Major repairs, such as replacing a damaged panel or repairing internal wiring, should be performed by qualified personnel. Improper repairs can compromise the safety and functionality of the cabinet.
- Part Replacement: When replacing parts, always use genuine replacement parts from the manufacturer or a reputable supplier. Using substandard parts can compromise the safety and longevity of the cabinet.
Environmental Considerations
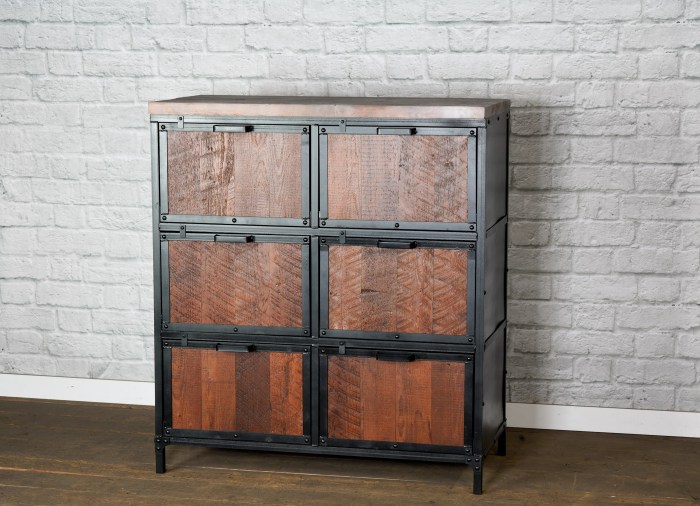
Source: combine9.com
Choosing industrial cabinets involves more than just functionality and durability; it also demands a thoughtful consideration of environmental impact throughout the product’s lifecycle, from manufacturing to disposal. Sustainable practices are increasingly important, not only for ethical reasons but also to meet growing regulatory requirements and reduce operational costs. This section explores the environmental implications of industrial cabinets and offers guidance on making eco-conscious choices.Selecting cabinets that align with specific environmental conditions is crucial for their longevity and to minimize potential environmental damage.
Exposure to harsh conditions can lead to premature cabinet failure, necessitating replacements and contributing to waste. Proper selection ensures both operational efficiency and environmental responsibility.
Industrial cabinets are known for their robust construction and utilitarian style. However, if you’re looking for something a bit more refined for your home theater, check out the sleek designs available in High-End Entertainment Center Cabinets. While industrial cabinets prioritize functionality, these offer a blend of style and practicality, showcasing how even high-end designs can incorporate industrial-inspired elements.
Environmental Impact of Manufacturing and Disposal
The manufacturing process of industrial cabinets consumes resources and generates waste. Materials extraction, energy use during fabrication, and transportation all contribute to a carbon footprint. Disposal also poses environmental challenges, as many cabinets contain materials that are not easily recyclable or biodegradable. However, manufacturers are increasingly adopting sustainable practices, such as using recycled materials, optimizing production processes to reduce energy consumption, and designing cabinets for easier disassembly and recycling at the end of their life.
Industrial cabinets are known for their rugged durability and utilitarian style. If you need something more tailored to your specific space, however, you might consider the sleek and organized options available with custom solutions like Custom Closet Cabinets. Whether it’s the raw aesthetic of industrial or the personalized fit of custom, the right cabinet choice significantly impacts your storage and overall space efficiency.
For example, some manufacturers utilize powder coating instead of liquid paint, reducing volatile organic compound (VOC) emissions. Companies are also exploring the use of bio-based materials and implementing closed-loop recycling systems to minimize waste.
Cabinet Selection for Specific Environmental Conditions
The choice of materials and construction techniques significantly influences a cabinet’s suitability for various environments. For high-humidity environments, cabinets made from stainless steel or powder-coated steel offer superior corrosion resistance. In extreme temperatures, cabinets with temperature-resistant seals and materials, such as certain types of plastics or specialized coatings, are necessary. For corrosive atmospheres, selecting cabinets constructed from materials like stainless steel or specialized polymers with high chemical resistance is vital.
Consideration must also be given to the cabinet’s sealing and ventilation to prevent moisture ingress or the build-up of corrosive gases. For example, a cabinet intended for a coastal location with high salinity should be made from marine-grade stainless steel.
Environmentally Friendly Materials for Industrial Cabinet Construction
Several materials offer a more environmentally friendly approach to industrial cabinet construction.
The selection of these materials should always consider the specific environmental conditions and the required performance characteristics of the cabinet.
- Recycled Steel: Utilizing recycled steel significantly reduces the demand for virgin materials and lowers energy consumption compared to using newly produced steel.
- Aluminum: Aluminum is highly recyclable and requires less energy to produce than steel, making it a relatively sustainable option.
- Bamboo: A rapidly renewable resource, bamboo offers a lightweight yet strong alternative for certain cabinet components, particularly in less demanding applications.
- Recycled Plastics: Using recycled plastics reduces reliance on petroleum-based resources and minimizes plastic waste in landfills.
- Sustainable Wood: Sourcing wood from responsibly managed forests ensures that the material is harvested sustainably, minimizing deforestation.
Cost and Value Analysis
Choosing the right industrial cabinet involves a careful consideration of not just the upfront cost, but also the long-term expenses and overall value it provides. This analysis will help you understand the total cost of ownership (TCO) for various cabinet types and how to assess their long-term value. Factors like material, features, and expected lifespan significantly impact the overall cost.Total Cost of Ownership (TCO) for Industrial Cabinets considers the initial purchase price, maintenance, repairs, and replacement costs over the cabinet’s lifetime.
A higher initial investment might be offset by lower maintenance costs and a longer lifespan, resulting in a lower TCO over time. Conversely, a cheaper initial purchase might lead to higher maintenance and replacement costs in the long run, increasing the overall TCO. Careful evaluation of these factors is crucial for making informed purchasing decisions.
TCO Comparison of Different Cabinet Types
The following table provides a cost breakdown for three common industrial cabinet types: basic steel, stainless steel, and custom-built. These figures are estimates and can vary based on size, features, and supplier. It is crucial to obtain quotes from multiple vendors for accurate pricing in your specific situation.
Cabinet Type | Initial Purchase Price (USD) | Annual Maintenance Cost (USD) | Estimated Lifespan (Years) | Approximate TCO (10 years, USD) |
---|---|---|---|---|
Basic Steel | 500 | 50 | 10 | 1000 |
Stainless Steel | 1500 | 25 | 20 | 1750 |
Custom-Built | 3000 | 100 | 25 | 5500 |
Evaluating Long-Term Value
Evaluating the long-term value of an industrial cabinet goes beyond just the TCO. It involves assessing its performance, reliability, and durability in relation to its intended use. A highly reliable cabinet minimizes downtime and potential production losses, adding significant indirect value. For example, a stainless steel cabinet in a food processing environment, despite a higher initial cost, offers superior corrosion resistance, ensuring hygiene and longevity, ultimately reducing the risk of costly contamination incidents.
Similarly, a robustly built cabinet in a harsh industrial setting will withstand wear and tear better, reducing repair and replacement costs. Durability and reliability translate into reduced operational disruptions and increased efficiency. These factors should be weighed against the initial cost to determine the true long-term value.
Last Point
Selecting the right industrial cabinet is a crucial decision impacting safety, efficiency, and long-term costs. From understanding the diverse materials and configurations available to mastering the nuances of safety regulations and maintenance, this guide provides a comprehensive overview. By carefully considering factors like environmental conditions, required capacity, and total cost of ownership, you can ensure your industrial cabinets provide years of reliable service, safeguarding your equipment and contributing to a safer, more productive work environment.
Remember, a well-chosen and properly maintained cabinet is an investment in efficiency and peace of mind.
Essential FAQs: Industrial Cabinets
What are the typical lifespan expectations for different types of industrial cabinets?
Lifespan varies greatly depending on material (steel cabinets may last 10-20 years, stainless steel longer), environment, and maintenance. Regular maintenance significantly extends lifespan.
How often should I perform preventative maintenance on my industrial cabinets?
A preventative maintenance schedule should include monthly inspections (visual checks for damage, loose connections), quarterly cleaning, and annual more thorough inspections involving component checks and potential adjustments.
Are there specific ventilation requirements for industrial cabinets housing electronics?
Yes, adequate ventilation is critical to prevent overheating. Consult manufacturer specifications and consider adding fans or other cooling systems as needed. Proper ventilation prevents equipment failure and potential fire hazards.
What are the implications of using the wrong NEMA rating for an industrial cabinet?
Using an incorrect NEMA rating exposes equipment to environmental hazards (water, dust, etc.), leading to malfunctions, damage, and potential safety risks. Always choose a NEMA rating appropriate for the environment.
How do I dispose of an old industrial cabinet responsibly?
Check local regulations for proper disposal of industrial waste. Many recycling centers accept scrap metal, and some companies offer cabinet recycling or repurposing services.